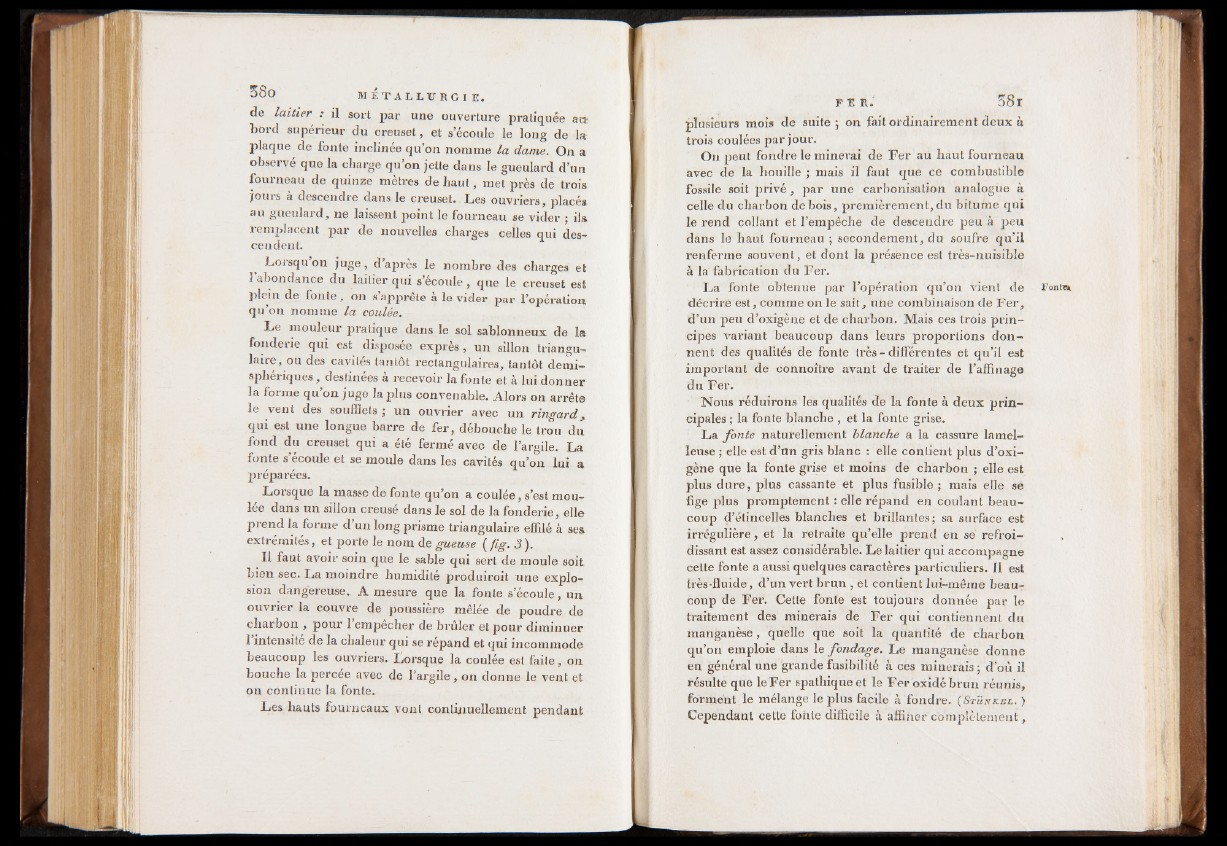
de laitier : il sort par une ouverture pratiquée sabord
supérieur du creuset, et s’écoule le long de 1*
plaque de fonte inclinée qu’on nomme la dame. On a
observé que la charge qu’on jette dans le gueulard d’un
fourneau de quinze mètres de haut, met près de trois
jours à descendre dans le creuset. Les ouvriers, placés
au gueulard, ne laissent point le fourneau se vider ; ils
remplacent par de nouvelles charges celles qui descendent.
Lorsqu on juge, d’après le nombre des charges et
1 abondance du laitier qui s’écoule, que le creuset est
plein de fonte, on s’apprête à le vider par l’opération,
qu’on nomme la coulée.
Le mouleur pratique dans le sol sablonneux de la
fonderie qui est disposée exprès, un sillon triangulaire,
ou des cavités tantôt rectangulaires, tantôt demi-
sphériques, destinées à recevoir la fonte et à lui donner
la forme qu’on juge la plus convenable. Alors on arrête
le vent des soufflets; un ouvrier avec un ringardg
qui est une longue barre de fer, débouche le trou du
fond du creuset qui a été fermé avec de l’argile. La
fonte s’écoule et se moule dans les cavités qu’on lui a
préparées.
Lorsque la masse de fonte qu’on a coulée, s’est moulée
dans un sillon creusé dans le sol de la fonderie, elle
prend la forme d’un long prisme triangulaire effilé à ses
extrémités, et porte le nom de gueuse (fig. 3 ).
Il faut avoir soin que le sable qui sert de moule soit
bien sec. La moindre humidité produiroit une explosion
dangereuse. A mesure que la fonte s’écoule, un
ouvrier la couvre de poussière mêlée de poudre de
charbon , pour 1 empecher de brûler et pour diminuer
1 intensité de la chaleur qui se répand et qui incommode
beaucoup les ouvriers. Lorsque la coulée est faite, on
bouche la percee avec de l’argile , on donne le vent et
on continue la fonte.
Les hauts fourneaux vont continuellement pendant
plusieurs mois de suite ; on fait ordinairement deux à
trois coulées par jour.
On peut fondre le minerai de Fer au haut fourneau
avec de la houille ; mais il faut que ce combustible
fossile soit privé, par une carbonisation analogue à
celle du charbon de bois, premièrement, du bitume qui
le rend collant et l’empêche de descendre peu à peu
dans le haut fourneau ; secondement, du soufre qu’il
renferme souvent, et dont la présence est très-nuisible
à la fabrication du Fer.
La fonte obtenue par l’opération qu’on vient de
décrirè est, comme on le sait, une combinaison<le Fer,
d’un peu d’oxigène et de charbon. Mais ces trois principes
variant beaucoup dans leurs proportions donnent
des qualités de fonte très - différentes et qu’il est
important de connoître avant de traiter de l’affinage
du Fer.
Nous réduirons les qualités de la fonte à deux principales
; la fonte blanche , et la fonte grise.
La fonte naturellement blanche a la cassure lamel-
leuse ; elle est d’an gris blanc : elle contient plus d’oxigène
que la fonte grise et moins de charbon ; elle est
plus dure, plus cassante et plus fusible ; mais elle se
fige plus promptement : elle répand en coulant beaucoup
d’étincelles blanches et brillantes; sa surface est
irrégulière, et la retraite qu’elle prend en se refroidissant
est assez considérable. Le laitier qui accompagne
cette fonte a aussi quelques caractères particuliers. Il est
très-fluide, d’un vert brun , et contient lui-même beaucoup
de Fer. Cette fonte est toujours donnée par le
traitement des minerais de Fer qui contiennent du
manganèse, quelle que soit la quantité de charbon
qu’on emploie dans le fondage. Le manganèse donne
en général une grande fusibilité à ces minerais ; d’où il
résulte que leFer spathiqueet le Fer oxidébrun réunis,
forment le mélange le plus facile à fondre. ( S t ü n k e l . )
Cependant cette fonte difficile à affiner complètement,
Fontes