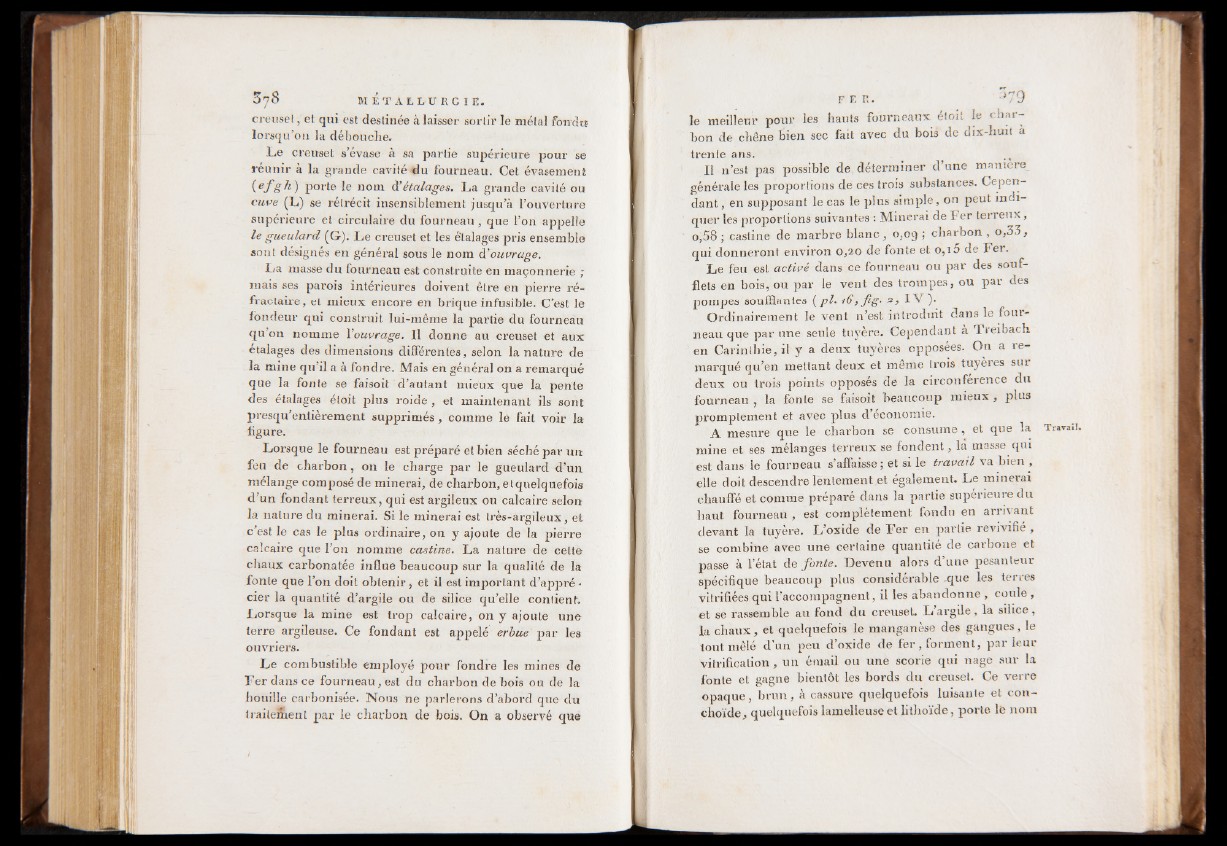
creuset, et qui est destinée à laisser sortir le métal fondu
lorsqu’on la débouche.
Le creuset s’évase à sa partie supérieure pour se
réunir à la grande cavité du fourneau. Cet évasement
( ef g h ) porte le nom d’étalages. La grande cavité ou
cuve (L) se rétrécit insensiblement jusqu’à l’ouverture
supérieure et circulaire du fourneau, que l’on appelle
le gueulard (G). Le creuset et les étalages pris ensemble
sont désignés en général sous le nom d’ouvrage.
La masse du fourneau est construite en maçonnerie ;
mais ses parois intérieures doivent être en pierre réfractaire,
et mieux encore en brique infusible. C’est le
fondeur qui construit lui-même la partie du fourneau
qu’on nomme l’ouvrage. Il don ne au creuset et aux
étalagés des dimensions différentes, selon la nature de
la mine qu’il a à fondre. Mais en général on a remarqué
que la fonte se faisoit d’autant mieux que la pente
des étalages étoit plus roide , et maintenant ils sont
presqu’entièrement supprimés, comme le fait voir la
figure.
Lorsque le fourneau est préparé et bien séché par un
feu de charbon, on le charge par le gueulard d’un
mélange composé de minerai, de charbon, et quelquefois
d’un fondant terreux, qui est argileux ou calcaire selon
la nature du minerai. Si le minerai est très-argileux, et
c’est le cas le plus ordinaire, on y ajoute de la pierre
calcaire que l’on nomme castine. La nature de celte
chaux carbonatée influe beaucoup sur la qualité de la
fonte que l’on doit obtenir, et il est important d’apprécier
la quantité d’argile ou de silice qu’elle contient.
Lorsque la mine est trop calcaire, on y ajoute une
terre argileuse. Ce fondant est appelé erbue par les
ouvriers.
Le combustible employé pour fondre les mines de
Fer dans ce fourneau, est du charbon de bois ou de la
houille carbonisée. Nous ne parlerons d’abord que du
traitement par le charbon de bois. On a observé que
le meilleur pour les hauts fourneaux étoit le charbon
de chêne bien sec fait avec du bois de dix-huit à
trente ans.
Il n’est pas possible de déterminer d une maniéré
générale les proportions de ces trois substances. Cependant
, en supposant le cas le plus simple, on peut indiquer
les proportions suivantes : Minerai de Fer terreux,
o,58 ; castine de marbre blanc, 0,09 ; charbon , o,33,
qui donneront environ 0,20 de fonte et 0,15 de Fer.
Le feu est activé dans ce fourneau ou par des soufflets
en bois, ou par le vent des trompes, ou par des
pompes soufflantes ( p l . i6,fig . 2, IV ) .
Ordinairement le vent n’est introduit dans le fourneau
que par une seule tuyère. Cependant a Treibach
en Carinlhie,il y a deux tuyères opposées. On a remarqué
qu’en mettant deux et même trois tuyères sur
deux ou trois points opposés de la circonférence du
fourneau , la fonte se faisoit beaucoup mieux , plus
promptement et avec plus d’économie.
A mesure que le charbon se consume, et que la
mine et ses mélanges terreux se fondent, là masse qui
est dans le fourneau s’affaisse ; et si le travail va bien ,
elle doit descendre lentement,et également. Le minerai
chauffé et comme préparé dans la partie supérieure du
haut fourneau , est complètement fondu en arrivant
devant la tuyère. L ’oxide de Fer en partie revivifié ,
se combine avec une certaine quantité de carbone et
passe à l’état d g fonte. Devenu alors d’une pesanteur
spécifique beaucoup plus considérable .que les terres
vitrifiées qui l’accompagnent, il les abandonne , coule ,
et se rassemble au fond du creuset. L argile, la silice,
la chaux, et quelquefois le manganèse des gangues, le
tout mêlé d’un peu d’oxide de fer, forment, parleur
vitrification, un émail ou une scorie qui nage sur la
fonte et gagne bientôt les bords du creuset. Ce verre
opaque, brun, à cassure quelquefois luisante et con-
choïde, quelquefois lamelleuse et lithoïde, porte lé nom
Trava