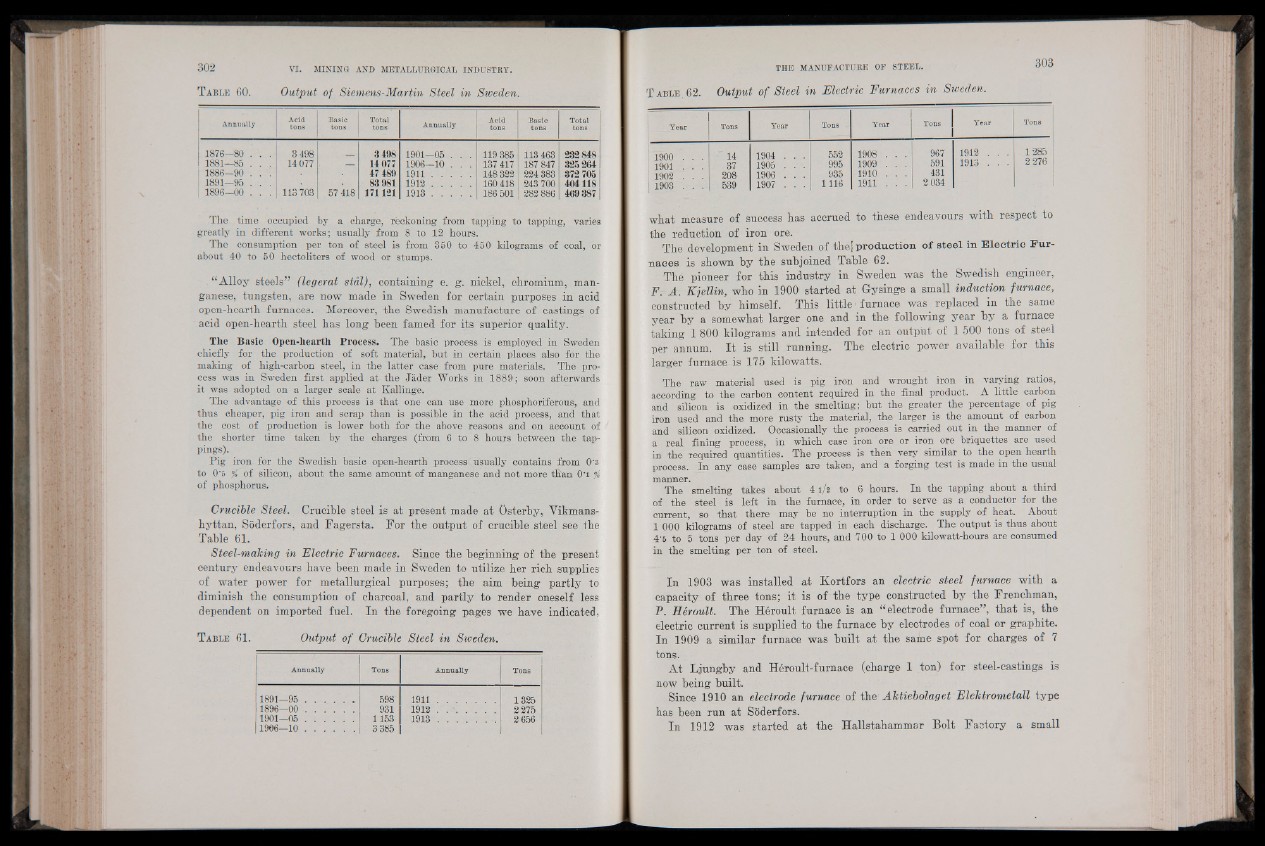
T able 60. Output of Siemens-Martin Steel in Sweden.
A, nnua,l,l y Atocnids
Basic
tons
Total
tons Annually Acid
tons
Basic
tons
Total
tons
1876—80 . . . 3 498 3498 1901—05 . . . 119 385 113 463 232 848
1881—85 . . . 14 077 — 14 077 1906—10 . . . 137 417 187 847 325 264
1886—90 . WÊÊSËSm 47 489 1 9 1 1 ................ 148 322 224 383 372 705
1891—95 . . . •SB 83 981 1 9 1 2 ................ 160 418 243 700 404118
1896—00 . . . 113 703 57 418 171121 1 9 1 3 ................ 186 501 282 886 469 387
The time occupied by a charge, reckoning from tapping to tapping, varies
greatly in different works; usually from 8 to 12 hours.
The consumption per ton of steel is from 350 to 450 kilograms of coal, or
about 40 to 50 hectoliters of wood or stumps.
“Alloy steels” (legerat stal), containing e. g. nickel, chromium, manganese,
tungsten, are now made in Sweden for certain purposes in acid
open-hearth furnaces. Moreover, the Swedish manufacture of castings of
acid open-hearth steel has long been famed for its superior quality.
The Basic Open-liearth Process. The basic process is employed in Sweden
chiefly for the production of soft material, but in certain places also for the
making of high-carbon steel, in the latter case from pure materials. The process
was in Sweden first applied at the Jader Works in 1889; soon afterwards
it was adopted on a larger scale at Kallinge.
The advantage of this process is that one can use more phosphoriferous, and
thus cheaper, pig iron and scrap than is possible in the acid process, and that
the cost of production is lower both for the above reasons and on account of
the shorter time taken by the charges (from 6 to 8 hours between the tappings).
Pig iron for the Swedish basic open-hearth process usually contains from 0'3
to 0'5 Yo of silicon, about the same amount of manganese and not more than O’l %
of phosphorus.
Crucible Steel. Crucible steel is at present made at Osterby, Vikmans-
hyttan, Soderfors, and Pagersta. For the output of crucible steel see the
Table 61.
Steel-making in Electric Furnaces. Since the beginning of the present
century endeavours have been made in Sweden to utilize her rich supplies
of water power for metallurgical purposes; the aim being partly to
diminish the consumption of charcoal, and partly to render oneself less
dependent on imported fuel. In the foregoing pages we have indicated,
T able 61. Output of Crucible Steel in Sweden.
Annually Tons Annually Tons
1891—95 .................... 598 1 9 1 1 ........................ 1325
1896—00 .................... 931 1912 . .................... 2 275
1901—05 .................... 1153 1 9 1 3 ....................... 2 656
1906—10 .................... 3 385
T able. 62. Output of Steel in Electric Furnaces in Sweden.
Year Tons Year Tons . Year Tons Year Tons
1900 . . . 1 1 4 1904 . . . 552 1908 . . . 967 1912 . . . 1*285
1901 . 1 . 37 1905 . . . 995 1909 . . . 591 1913 . . . 2 276
! 1902 . . . 208 1906 . . . 935 1910 . . . 431
1903 . . . 539 1907 . . . 1116 1911 . . . 2 034
what measure of success has accrued to these endeavours with respect to
the reduction of iron ore.
The development in Sweden of the! production of steel in Electric Furnaces
is shown by the subjoined Table 62.
The pioneer for this industry in Sweden was the Swedish engineer,
F. A. Kjellin, who in 1900 started at Gysinge a small induction furnace,
constructed by himself. This little 1 furnace was replaced in the same
year by a somewhat larger one and in the following year by a furnace
taking 1 800 kilograms and intended for an output of 1 500 tons of steel
per annum. It is still running. The electric power available for this
larger furnace, is 175 kilowatts.
The raw material used is pig iron and wrought iron in varying ratios,
according to the carbon content required in the final product. A little carbon
and silicon is oxidized in the smelting; but the greater the percentage of pig
iron used and the more rusty the material, the larger is the amount of carbon
and silicon oxidized. Occasionally the process is earned out in the manner of
a real fining process, in which case iron ore or iron ore briquettes are used
in the required quantities. The process is then very similar to the open hearth
process. In any case samples are taken, and a forging test is made in the usual
manner. ■ ■ ■
The smelting takes about 4i /> to 6 hours. In the tapping about a third
of the steel is left in the furnace, in order to serve as a conductor for the
current, so that there may be no interruption in the supply of heat. About
1 000 kilograms of steel are tapped in each discharge. The output is thus about
4-5 to 5 tons per day of 24 hours, and 700 to 1 000 kilowatt-hours are consumed
in the smelting per ton of steel.
In 1903 was installed at Kortfors an electric steel furnace with a
capacity of three tons; it is of the type constructed by the Frenchman,
P. Hérault. The Héroult furnace is an “ electrode furnace”, that is, the
electric current is supplied to the furnace by electrodes of coal or graphite.
In 1909 a similar furnace was built at the saine spot for charges of 7
tons.
At Ljungby and Héroult-fumace (charge 1 ton) for steel-castings is
now being built.
Since 1910 an electrode furnace of the Aktiebolaget Elektrometall type
has been run at Soderfors.
In 1912 was started at the Hallstahammar Bolt Factory a small