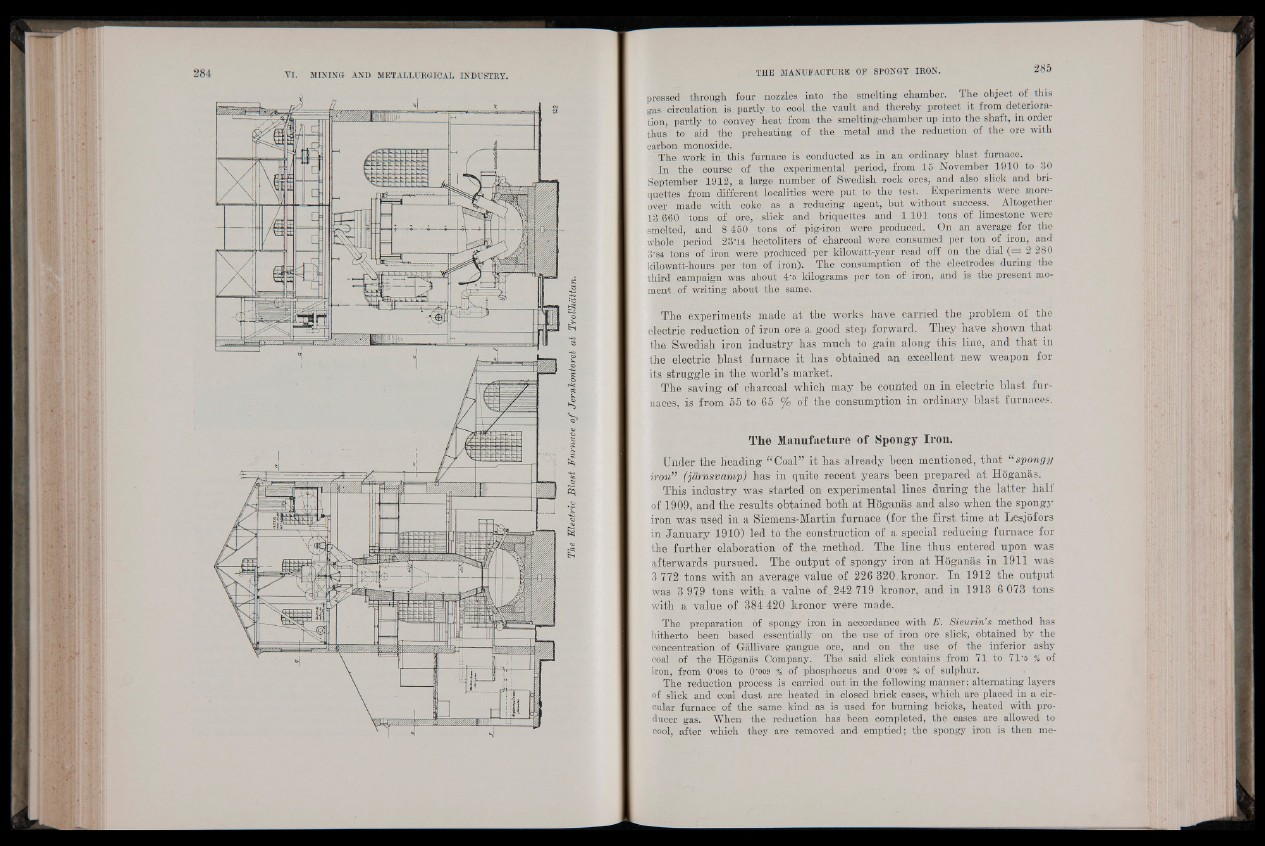
The Electric Blast Furnace of Jernkontoret at Trollhättan.
pressed through four nozzles into the smelting chamber. The object of this
gas circulation is partly to cool the vault and thereby protect it from deterioration,
partly to convey heat from the smelting-chamber up into the shaft, in order
thus to aid the preheating of the metal and the reduction of the ore with
carbon monoxide.
The work in this furnace is conducted as in an ordinary blast furnace.
In the course of the experimental period, from 15 November 1910 to 30
September 1912,. a large number of Swedish rock ores, and also slick and briquettes
from different localities were put to the t e s t ., Experiments were moreover
made with coke as a reducing agent, but without success. Altogether
13 660 tons o f ore, .slick and briquettes and -1101 tons of limestone were
smelted, and 8.450 tons of pig-iron were produced. On an average for the
whole period 23*« hectoliters of charcoal were consumed per ton of iron, and
3*81 tons of iron were produced per kilowatt-year read off on the dial ( = 2 280
kilowatt-hours per ton of iron). The consumption of the electrodes during the
third campaign was about 4*5 kilograms per ton of iron, and is the present moment
of writing about the same.
The experiments made at the works have carried the problem of the
electric reduction of iron ore a good step forward. They have shown that
the Swedish iron industry has much to gain along this line, and that in
the electric blast furnace it has obtained an excellent new weapon for
its struggle in the world’s market.
The saving of charcoal which may be counted on in electric blast furnaces,
is from 5 5 to 65 % of the consumption in ordinary blast furnaces.
The Manufacture of Spongy Iron.
Under the heading “Coal” it has already been mentioned, that “ spongy
iron” (jdrnsvamp) has in quite recent years been prepared at Hoganas.
This industry was started on experimental lines during the latter half
of 1909, and the results obtained both at Hoganas and also when the spongy
iron was used in a Siemens-Martin furnace (for the first time at Lesjofors
in January 1910) led to the construction of a special reducing furnace for
the further elaboration of the. method. The line thus entered upon was
afterwards pursued. The output of spongy iron at Hoganas in 1911 was
3 772 tons with an average value of 226 320.kronor. In 1912 the output
was 3 979 tons with, a value of . 242 719 kronor, and in 1913 6 073 tons
with a value of 384 420 kronor were made..
The preparation ¿SE spongy iron in accordance with E. Sieurin’s method has
hitherto been based essentially on the use of iron ore slick, obtained by the
concentration of Gallivare gangue ore, and on the use of the inferior ashy
coal of the Hoganas Company. The said slick contains from 71 to 71*5 % of
iron, from 0*008 to 0*009 % of phosphorus and O'oos % of sulphur.
The reduction process is carried out in the following manner: alternating layers
of slick and coal dust are heated in closed brick cases, which are placed in a circular
furnace of the same kind as is used for burning bricks, heated with producer
gas. When the reduction has been completed, the cases are allowed to
cool, after which they are removed and emptied; the spongy iron is then me