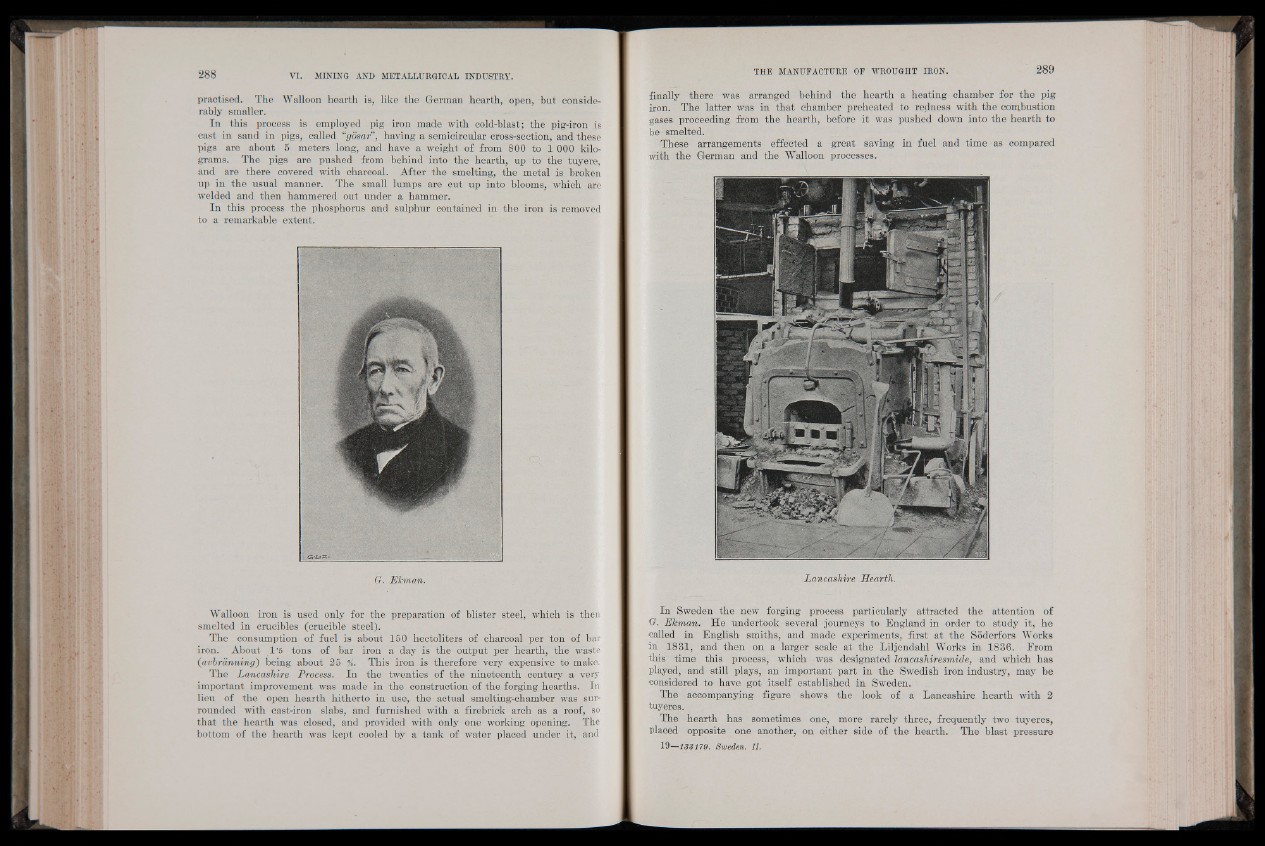
practised. The Walloon hearth is, like the German hearth, open, but considerably
smaller.
In this process is employed pig iron made with cold-blast; the pig-iron is
cast in sand in pigs, called “gosar”, having a semicircular cross-section, and these
pigs are about 5 meters long, and have a weight of from 800 to 1 000 kilograms.
The pigs are pushed from behind into the hearth, up to the tuyere,
and are there covered with charcoal. After the smelting, the metal is broken
up in the usual manner. The small lumps are cut up into blooms, which are
welded and then hammered out under a hammer.
In this process the phosphorus and sulphur contained in the iron is removed
to a remarkable extent.
G. Ekman.
Walloon iron is used only for the preparation of blister steel, which is then
smelted in crucibles (crucible steel).
The consumption of fuel is about 150 hectoliters of charcoal per ton of bar
iron. About 1 o tons of bar iron a day is the output per hearth, the waste
(avbrdnning) being about 25 %. This iron is therefore very expensive to make.
The Lancashire Process. In the twenties of the nineteenth century a very
important improvement was made in the construction of the forging hearths. In
lieu of the open hearth hitherto in use, the actual smelting-chamber was surrounded
with cast-iron slabs, and furnished with a firebrick arch as a roof, so
that the hearth was closed, and provided with only one working opening. The
bottom of the hearth was kept cooled by a tank of water placed under it, and
finally there was arranged behind the hearth a heating chamber for the pig
iron. The latter was in that chamber preheated to redness with the combustion
gases proceeding from the hearth, before it was pushed down into the hearth to
be smelted.
These arrangements effected a great saving in fuel and time as compared
with the German and the. Walloon processes.
Lancashire Hearth.
In Sweden the new forging process particularly attracted the attention of
G. Ekman. He undertook several journeys to England in order to study it, he
called in English smiths, and made experiments, first at the Soderfors Works
in 1831, and then on a larger scale at the Liljendahl Works in 1836. From
this time this process, which was designated lancashiresmide, and which has
played, and still plays, an important part in the Swedish iron industry, may be
considered to have got itself established in Sweden.
The accompanying figure shows the look of a Lancashire hearth with 2
tuyeres.
The hearth has sometimes one, more rarely three, frequently two tuyeres,
placed opposite one another, on either side of the hearth. The blast pressure