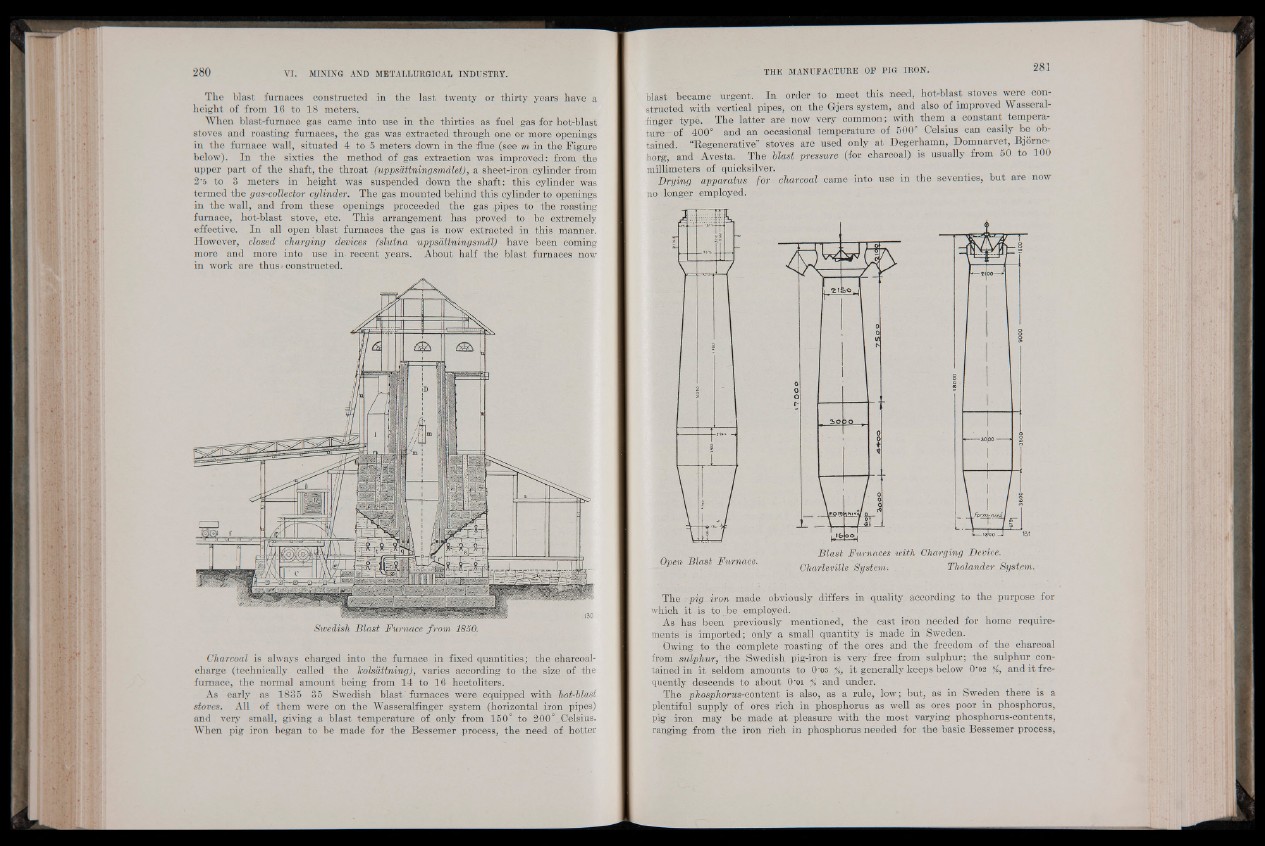
The blast furnaces constructed in the last twenty or thirty years have a
height of from 16 to 18 meters.
When blast-furnace gas came into use in the thirties as fuel gas for hot-blast
stoves and roasting furnaces, the gas was extracted through one or more openings
in the furnace wall, situated 4 to 5 meters down in the flue (see m in the Figure
below). In the sixties the method of gas extraction was improved: from the
upper part of the shaft, the throat (uppsattningsmdlet) , a sheet-iron cylinder from
2-5 to 3 meters in height was suspended down the shaft: this cylinder was
termed the gas-collector cylinder. The gas mounted behind this cylinder to openings
in the wall, and from these openings proceeded the gas pipes to the roasting
furnace, hot-blast stove, etc. This arrangement has proved to be extremely
effective. In all open blast furnaces the gas is now extracted in this manner.
However, closed charging devices (slutna uppsattningsmal) have been coming
more and more into use in recent years. About half the blast furnaces now
in work are thus» constructed.
Swedish Blast Furnace from 1850.
Charcoal is always charged into the furnace in fixed quantities; the charcoal-
chaxge (technically called the TcolsattningJ, varies according to the size of the
furnace, the normal amount being from 14 to 16 hectoliters.
As early as 1835 35 Swedish blast furnaces were equipped with hot-blast
stoves. All of them were on the Wasseralfinger system (horizontal iron pipes)
and very small, giving a blast temperature of only from 150° to 200° Celsius.
When pig iron began to be made for the Bessemer process, the need of hotter
blast became urgent. In order to meet this need, hot-blast stoves were constructed
with vertical pipes, on the Gjers system, and also of improved Wasseral-
finger type. The latter are now very common; with them a constant temperature
of 400° and an occasional temperature of 500“ Celsius can easily be obtained.
“Regenerative” stoves are used only at Degerhamn, Domnarvet, Bjome-
borg, and Avesta. The blast pressure (for charcoal) is usually from 50 to 100
millimeters of quicksilver.
Drying apparatus for charcoal came into use in the seventies, but are now
no longer employed.
Blast Furnaces with Charging Device..
Open Blast Furnace. CharleviUe. System-. : Tholander System.
The . pig iron made obviously differs in quality according to the purpose for
which i t .is to be employed. •
As has been previously mentioned, the cast iron needed for home requirements
is imported; only a small quantity is made in Sweden.
Owing to the complete roasting of the ores and the freedom of the charcoal
from sulphur, the Swedish pig-iron is very free from sulphur; the sulphur contained
in it .seldom amounts to 0'03 %, it generally keeps below O'oa / , and it frequently
descends to about O’oi % and under.
The phosphorus-content is also, as a rule, low; but, as in Sweden there is a
plentiful supply of ores rich in phosphorus as well as ores poor in phosphorus,
pig iron may be made at pleasure with the most varying phosphorus-contents,
ranging from the iron rich in phosphorus needed for the basic Bessemer process,