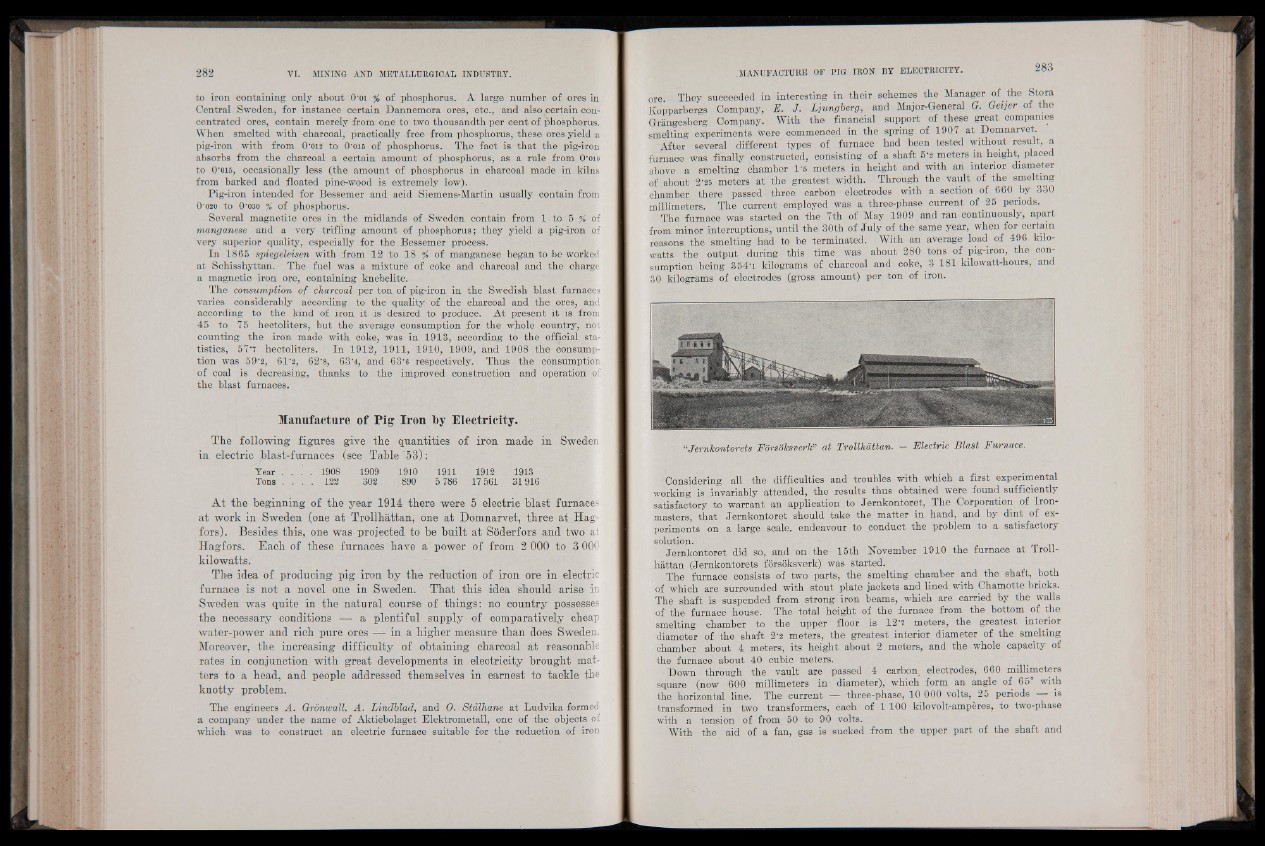
to iron containing only about O'oi % of phosphorus. A large number of ores in
Central Sweden, for instance certain Dannemora ores, etc., and also .certain concentrated
ores, contain merely from one to two thousandth per cent of phosphorus.
When smelted with charcoal, practically free from phosphorus, these ores yield a
pig-iron with from O'oia to O'Olo of phosphorus. The fact is that the pig-iron
absorbs from the charcoal a certain amount of phosphorus, as a rule from O'oio
to O'015, occasionally less (the amount of phosphorus in charcoal made in kilns
from barked and floated pine-wood is extremely low).
Pig-iron intended for Bessemer and acid Siemens-Martin usually contain from
O'oao to 0'030 % of phosphorus.
Several magnetite ores in the midlands of Sweden contain from 1 to 5 % of
manganese and a very trifling amount of phosphorus; they yield a pig-iron of
very superior quality, especially for the Bessemer process.
In 1865 spiegeleisen with from 12 to 18 % of manganese began to be worked
at Schisshyttan. The fuel was a mixture of coke and charcoal and the charge
a magnetic iron ore, containing knebelite.
The consumption of charcoal per ton of pig-iron in the Swedish blast furnaces
varies considerably according to the quality of the charcoal and the ores, and
according to the kind of iron it is desired to produce. At present it is from
45 to 75 hectoliters, hut the average consumption for the whole country, not
counting the iron made with coke, was in 1913, according to the official statistics,
57'7 hectoliters. In 1912, 1911, 1910, 1909, and 1908 the consumption
was 59'2, 61'2, 62'8, 63'4, and 63'6 respectively. Thus the consumption
of coal is decreasing, thanks to the improved construction and operation |of
the blast furnaces.
Manufacture of Pig Iron by Electricity.
The following figures give the quantities of iron made in Sweden
in electric blast-furnaces (see Table 53):
Year . . .’ . 1908 1909 1910 1911 1912 1913
Tons . . . . 122 302 890 5786 17561 31916
At the beginning of the year 1914 there were 5 electric blast furnaces
at work in Sweden (one at Trollhattan, one at Domnarvet, three at Hag-
fors). Besides this, one was-projected to be built at Soderfors and two at
Hagfors. Each of these furnaces have a power of from 2 000 to 3 000
kilowatts.
The idea of producing pig iron by the reduction of iron ore in electric
furnace is not a novel one in Sweden. That this idea should arise sin
Sweden was quite in the natural course of things: no country possesses
the necessary conditions — a plentiful supply of comparatively cheap
water-power and rich pure ores — in a higher measure than does Sweden.
Moreover, the increasing difficulty of obtaining charcoal at reasonable
rates in conjunction with great developments in electricity brought matters
to a head, and people addressed themselves in earnest to tackle the
knotty problem.
The engineers A. Gronwall, A. Lindblad, and O. Stalhane at Ludvika formed
a company under the name of Aktiebolaget Elektrometall, one of the objects of
which was to construct an electric furnace suitable for the reduction of iron
ore They succeeded in interesting in their schemes the Manager of the Stora
Kopparbergs Company, E. J. Ljungberg, and Major-General O. Oeijer of the
Grangesberg Company. With the financial support of these great companies
smelting experiments were commenced in the spring of 1907 at Domnarvet.
After several different types of furnace had been tested without result, a
furnace was finally constructed, consisting of a shaft 5's meters in height, placed
above a smelting chamber 1'5 meters in height and with an interior diameter
of about 2*25 meters at the greatest width. Through the vault of the smelting
chamber there passed three carbon electrodes with a section of 660 by 330
millimeters. The current employed was a three-phase current of 25 periods.
The furnace was started on the 7th of May 1909 and ran continuously, apart
from minor interruptions, until the 30th of July of the same year, when for certain
reasons the smelting had to he terminated. With an average load of 496 kilowatts
the output during this time was about 280 tons of pig-iron, the consumption
being 354'i kilograms of charcoal and coke, _ 3 181 kilowatt-hours, and
30 kilograms of electrodes (gross amount) per ton of iron.
“Jernkontorets Forsoksverk” at Trollhattan. — Electric Blast Furnace.
Considering all the difficulties and troubles with which a first experimental
working is invariably attended, the results thus obtained were found sufficiently
satisfactory to warrant an application to Jernkontoret, The Corporation of Ironmasters,
that Jernkontoret should take the matter in hand, and by dint of experiments
on a large scale, endeavour to _conduct the problem to a satisfactory
solution.
Jernkontoret did so, and on the 15th November 1910 the furnace at Trollhattan
(Jernkontorets forsoksverk) was started.
The furnace consists of two parts, the smelting chamber and the shaft, both
of which are surrounded with stout plate jackets and lined with Chamotte bricks.
The shaft is suspended from strong iron beams, which are carried by the walls
of the furnace house. The total height of the furnace from the bottom of the
smelting chamber to the upper floor is 12"7 meters, the greatest interior
diameter of the shaft 2'2 meters, the greatest interior diameter of the smelting
chamber about 4 meters, its height about 2 meters, and the whole capacity of
the furnace about 40 cubic meters.
Down through the vault are passed 4 carbon electrodes, 660 millimeters
square (now 600 millimeters in diameter), which form an angle of 65° with
the horizontal line. The current — three-phase, 10 000 volts, 25 periods — is
transformed in two transformers, each of 1 100 kilovolt-amperes, to two-phase
with a tension of from 50 to 90 volts.
With the aid of a fan, gas is sucked from the upper part of the shaft and