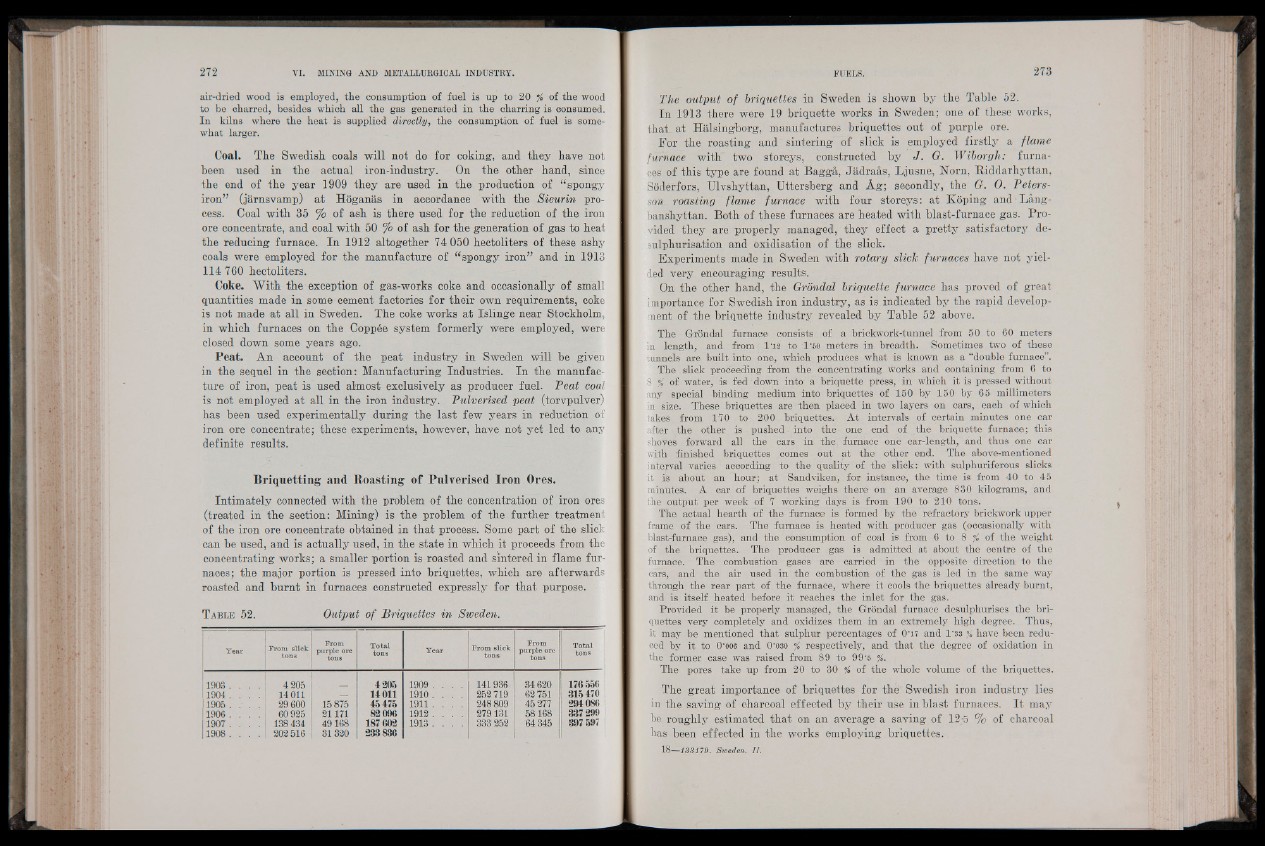
air-dried wood is employed, the consumption of fuel is up to 20 % of the wood
to be charred, besides which all the gas generated in the charring is consumed.
In kilns where the heat is supplied directly, the consumption of fuel is somewhat
larger.
Coal. The Swedish coals will not do for coking, and they have not
been used in the actual iron-industry. On the other hand, since
the end of the year 1909 they are used in the production of “spongy
iron” (jarnsvamp) at Hoganas in accordance with the Sieurin process.
Coal with 35 % of ash is there used for the reduction of the iron
ore concentrate, and coal with 50 % of ash for the generation of gas to heat
the reducing furnace. In 1912 altogether 74 050 hectoliters of these ashy
coals were employed for the manufacture of “ spongy iron” and in 1913
114 760 hectoliters.
Coke. With the exception of gas-works coke and occasionally of small
quantities made in some cement factories for their own requirements, coke
is not made at all in Sweden. The coke works at Islinge near Stockholm,
in which furnaces on the Coppee system formerly were employed, were
closed down some years ago.
Peat. An account of the peat industry in Sweden will be given
in the sequel in the section: Manufacturing Industries. In the manufacture
of iron, peat is used almost exclusively as producer fuel. Teat coal
is not employed at all in the iron industry. Pulverised peat (torvpulver)
has been used experimentally during the last few years in reduction of
iron ore concentrate; these experiments, however, have not yet led to any
definite results.
Briquetting and Boasting of Pulverised Iron Ores.
Intimately connected with the problem of the concentration of iron ores
(treated in the section: Mining) is the problem of the further treatment
of the iron ore concentrate obtained in that process. Some part of the slick
can be used, and is actually used, in the state in which it proceeds from the
concentrating works; a smaller portion is roasted and sintered in flame furnaces;
the major portion is pressed into briquettes, which are afterwards
roasted and burnt in furnaces constructed expressly for that purpose.
T able 52. Output of Briquettes in Sweden.
Year From slick
tons
From
purple ore
tons
Total
tons Year From slick
tons
From
purple ore
tons
Total
tons
1903 . . . . 4 205 4 205 1909 . . . . 141936 34 620 176556
1904 . . . . 14 011 BIBBS v 14011 1910 . . . . 252 719 62 751 315470
1905 . . . . 29 600 15 875 45 475 1911 . . . . 248 809 45 277 294 086
1906 . . . . 60 925 21171 82 096 1912 . . . . 279131 58168 337 299
1907 . . . .
138 434
49168
187 602
1913 . . . . 333 252 64 345 397 597
1908 . . . .
202 516
31320
233836
The output of briquettes in Sweden is shown by the Table 52.
In 1913 there were 19 briquette works in Sweden; one of these works,
that at Halsingborg, manufactures briquettes out of purple ore.
l ’or the roasting and sintering of slick is employed firstly a flame
furnace with two storeys, constructed by J . G. Wiborgh: furnaces
of this type are found at Baggâ, Jâdraâs, Ljusne, Norn, Riddarhyttan,
Soderfors, Ulvshyttan, Uttersberg and Âg; secondly, the G. O. Peters-
son. roasting flame furnace with four storeys: at Koping and - Lâ-ng-
banshyttan. Both of these furnaces are heated with blast-furnace gas. Provided
they are properly managed, they effect a pretty satisfactory de-
sulphurisation and oxidisation of the slick.
Experiments made in Sweden with rotary slick furnaces have not y ielded
very encouraging results.
On the other hand, the Grondai briquette furnace has proved of great
importance for Swedish iron industry, as is indicated by the rapid development
of the briquette industry revealed by Table 52 above.
The Grondai furnace consists of a brickwork-tunnel from 50 to 60 meters
in length, and from l'is to 1 ’60 meters in breadth. Sometimes two of these
tunnels are built into one, which produces what is known as a “double furnace”.
The slick proceeding from the concentrating works and containing from 6 to
81 % of water, is fed down into a briquette press, in which it is pressed without
any special binding medium into briquettes of 150 by 150 by 65 millimeters
in size. These briquettes are then placed in two layers on cars, each of which
takes from 170 t0: 200 briquettes. At intervals of certain minutes one car
after >ithe other is pushed ■ into the- one . end of the briquette furnace; this
shoves forward all the cars in the furnace one car-length, and thus one car
with finished briquettes comes out at the other end. The above-mentioned
interval varies according to the quality of the ' slick : with sulphuriferous slicks
it is about an hour; at Sandviken, for instance, the time is from 40 to 45
minutes. A car of briquettes weighs there on an average 830 kilograms, and
the output per week of 7 working days is from 190 to 210 tons.
The actual hearth of the furnace is formed by the refractory brickwork upper
frame of the cars. The furnace is heated with producer gas (occasionally with
blast-furnace gas), and the consumption of coal is from 6 to 8 % of the weight
of the briquettes. The producer gas is admitted at about the centre of the
furnace,' The combustion gases are carried in the opposite direction to the
ears, and the air used in the combustion of the gas is led in the same way
through the rear part of the furnace, where it cools the briquettes already burnt,
and is itself heated before it reaches the inlet for the gas.
Provided it be properly managed, the Grondai furnace desulphurises the briquettes
very completely and oxidizes them in an extremely high degree. Thus,
it may be mentioned that sulphur percentages of O'iï and 1 ‘33 % have been reduced
by it to 0 ' o o g and 0 ‘ 0 3 0 ‘/o respectively, and that the degree of oxidation in
the former case was raised from 89 to 99'6 %.
The pores take up from 20 to 80 % of the whole volume of the briquettes.
The great importance of briquettes for thé Swedish iron industry lies
in the saving of oharcoal effected by their use in blast furnaces. It may
be roughly estimated that on an average a saving of 12-5 % of charcoal
has been effected in the works employing briquettes..