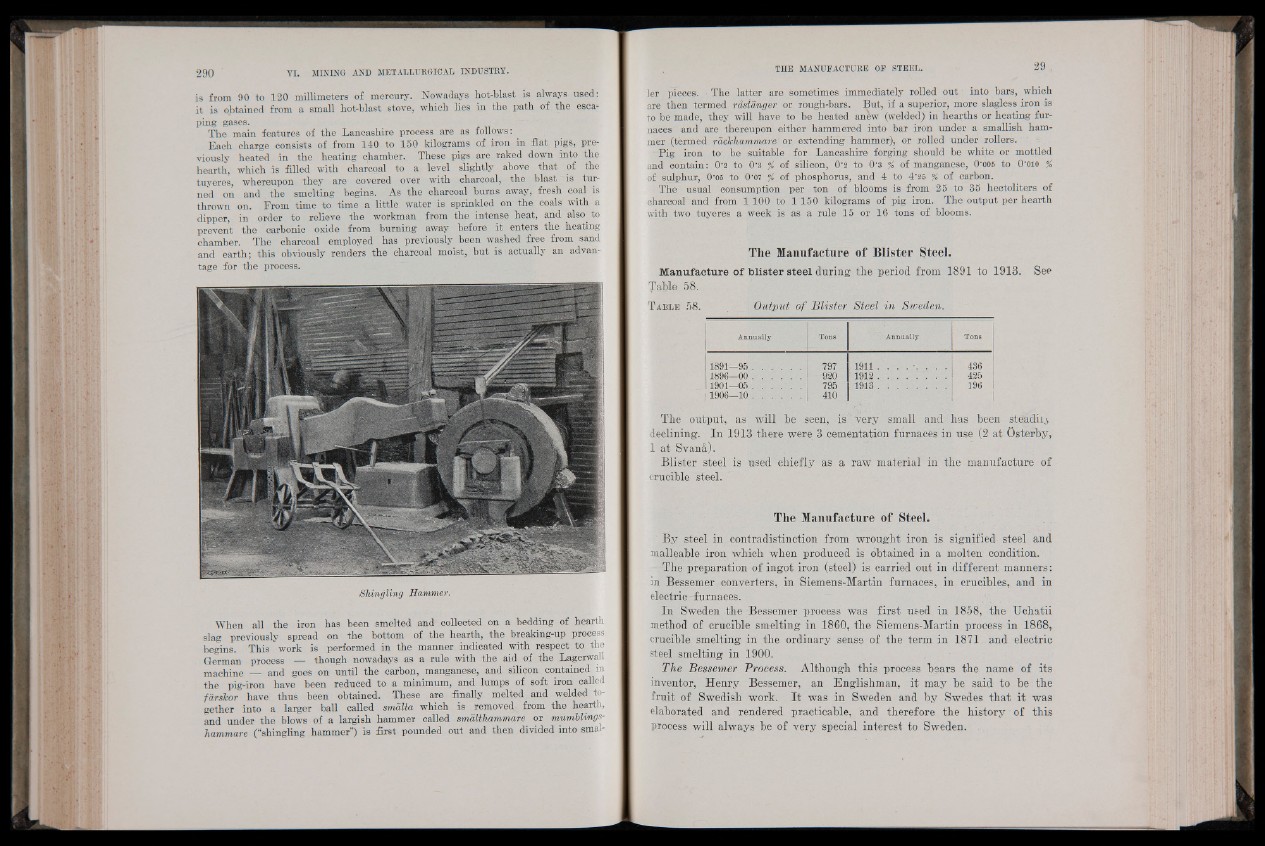
is from 90 to 120 millimeters of mercury. Nowadays hot-blast is always used:
it is obtained from a small hot-blast stove, which lies in the path of the esca-
ping gases.
The main features of the Lancashire process are as follows:
Each charge consists of from 140 to 150 kilograms of iron in flat pigs, previously
heated in the heating chamber. These pigs are raked down into the
hearth, which is filled with charcoal to a level slightly above that of the
tuyeres, whereupon they are covered over with charcoal, the blast is turned
on and the smelting begins. As the charcoal burns away, fresh coal is
thrown on. From time to time a little water is sprinkled on the coals with a
dipper, in order to relieve the workman from the intense heat, and also^ to
prevent the carbonic oxide from burning away before it enters the heating
chamber. The charcoal employed has previously been washed free from sand
and earth; this obviously renders the charcoal moist, but is actually an advantage
for the process.
Shingling Hammer.
When all the iron has been smelted and collected on a bedding of hearth
slag previously spread on the bottom of the hearth, the breaking-up process
begins. This work is performed in the manner indicated with respect to the
German process — though nowadays as a rule with the aid of the Lagerwall
machine — and goes on until the carbon, manganese, and silicon contained in
the pig-iron have been reduced to a minimum, and lumps of soft iron called
fdrskor have thus been obtained. These are finally melted and welded together
into a larger ball called smatta which is removed, from the hearth,
and under the blows of a largish hammer called smalthammare or mumblings-
hammare (“shingling hammer”) is first pounded out and then divided into smaller
pieces. The latter are sometimes immediately rolled out into bars, which
are then termed rasianger or rough-bars. But, if a superior, more slagless iron is
to be made, they will have to be heated anew (welded) in hearths or heating furnaces
and are thereupon either hammered into bar iron under a smallish hammer
(termed rackhammare' or extending hammer), or rolled under rollers.
Pig iron to~ be suitable for Lancashire forging should be white or mottled
and contain: 0'2 to 0’3 °/„ of silicon, 0'2 to 0’S % of manganese, 0’oos to O'oio %
of sulphur, 0'05 to 0'07 % of phosphorus,“ and 4 to 4 ’26 % of carbon.
The usual consumption per ton of blooms is from 25 to 35 hectoliters of
charcoal and from 1 1 0 0 to 1 1 5 0 kilograms of pig iron. The output per hearth
with two tuyeres a week is as a rule 15 or 16 tons of blooms.
The Manufacture of Blister Steel.
Manufacture of blister steel during the period from 1891 to 1913. See
Table 58.
T able 58. Output of Blister Steel in Sweden. .
Annually Tons ; Annually Tons
1891—95 ................ 797 1911 . . . . . . . . . 436
1896—00 .................... 920 ’1 9 1 2 ............................ 425
1901—05 . 1 1 1 1 . 795 1913 . : .................... 196 1
1906—10 .................... 410
The output, as will he seen, i s ‘Very small and has been steadily
declining. In 1913 there were 3 cementation furnaces in use (2 at Osterby,
1 at Svana).
Blister steel is used chiefly as a raw material in the manufacture of
crucible steel.
The Manufacture of Steel.
By steel in contradistinction from wrought iron is signified steel and
malleable iron which when produced is obtained in a molten condition.
The preparation of ingot iron (steel) is carried out in different manners:
in Bessemer converters, in Siemens-Martin furnaces, in crucibles, and in
electric furnaces.
In Sweden the Bessemer process was first used in 1858, the Uchatii
method of crucible smelting in 1860, the Siemens-Martin process in 1868,
crucible smelting in the ordinary sense of the term in 1871 and electric
steel smelting in 1900.
The Bessemer Process. Although this process bears the name of its
inventor, Henry Bessemer, an Englishman, it may be said to be the
fruit of Swedish work. It was in Sweden and by Swedes that it was
elaborated and rendered practicable, and therefore the history of this
process will always be of very special interest to Sweden.