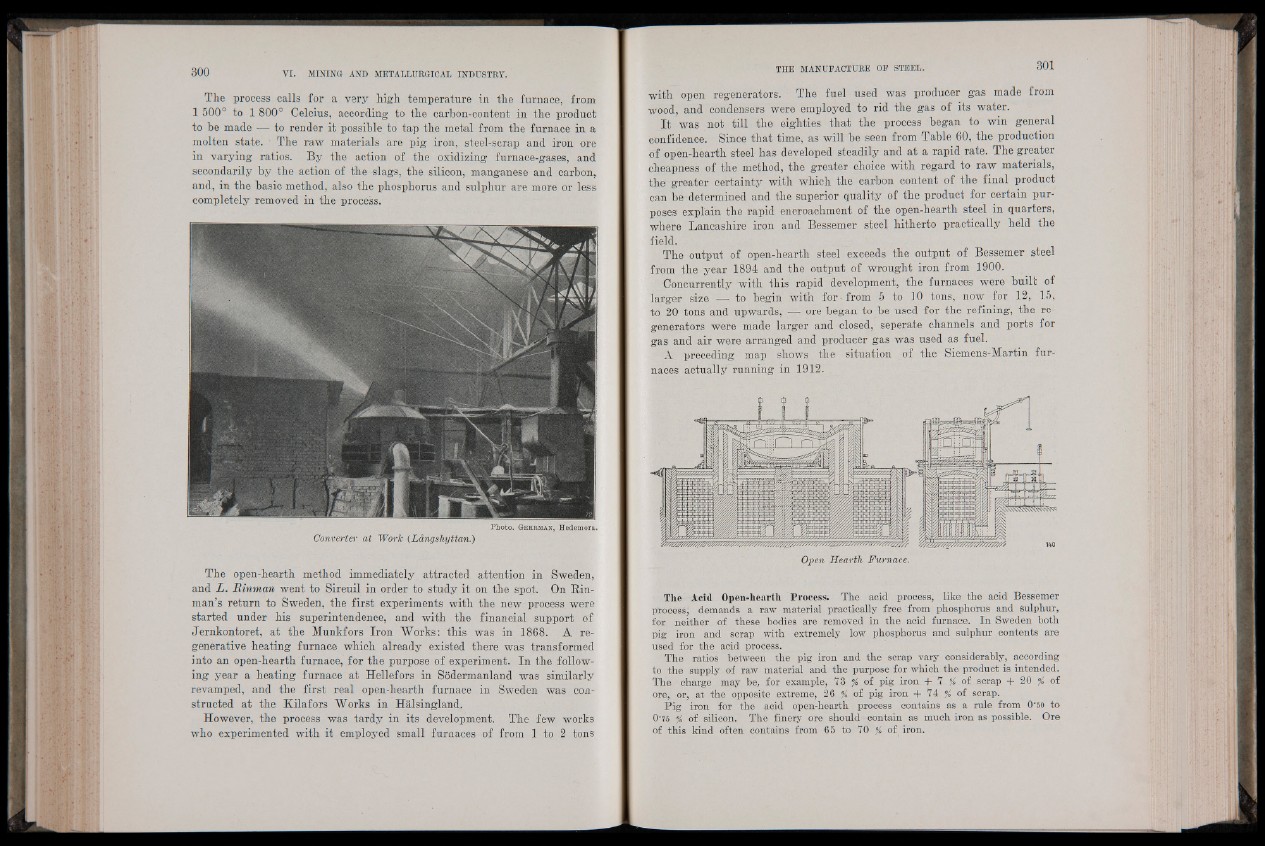
The process calls for a very high temperature in the furnace, from
1 500° to 1 800° Celcius, according to the carbon-content in the product
to be made -— to render it possible to tap the metal from the furnace in a
molten state. - The raw materials are pig iron, steel-scrap and iron ore
in varying ratios. By the action of the oxidizing furnace-gases, and
secondarily by the action of the slags, the silicon, manganese and carbon,
and, in the basic method, also the phosphorus and sulphur are more or less
completely removed in the process.
Photo. Geh rm a n , Hedemora.
Converter at Work {Langshyttan.)
The open-hearth method immediately attracted attention in Sweden,
and L. Rinman went to Sireuil in order to study it on the spot. On Bin-
man’s return to Sweden, the first experiments with the new process were
started under his superintendence, and with the financial support of
Jernkontoret, at the Munkfors Iron Works: this was in 1868. A regenerative
heating furnace which already existed there was transformed
into an open-hearth furnace, for the purpose of experiment. In the following
year a heating furnace at Hellefors in Sodermanland was similarly
revamped, and the first real open-hearth furnace .in Sweden was constructed
at the Kilafors Works in Halsingland,
However, the process was tardy in its development. The few works
who experimented with it employed small furnaces of from 1 to 2 tons
with open regenerators. The fuel used was producer gas made from
wood, and condensers were employed to rid the gas of its water.
It was not till the eighties that the process began to win general
confidence. Since that time, as will be seen from Table 60, the production
of open-hearth steel has developed steadily and at a rapid rate. The greater
cheapness of the method, the greater choice with regard to raw materials,
the greater certainty with which the carbon content of the final product
can be determined and the superior quality of the product for certain purposes
explain the rapid encroachment of the open-hearth steel in quarters,
where Lancashire iron and Bessemer steel hitherto practically held the
field,
The output of open-hearth steel exceeds the output of Bessemer steel
from the year 1894 and the output of wrought iron from 1900.
Concurrently with this rapid development, the furnaces were built of
larger size — to begin with for-from 5 to 10 tons, now for 12, 1.5,
to 2 0 tons and upwards, — ore began to be used for the refining, the regenerators
were made larger and closed, seperate channels and ports for
gas and air were arranged and producer gas was used as fuel.
A preceding map shows the situation of the Siemens-Martin furnaces
actually running in 1912.
Open Hearth Furnace.
The Acid Open-hearth Process. The acid process, like the acid Bessemer
process; demands a raw material practically free from phosphorus and Sulphur,
for neither of these bodies are removed in the acid furnace. In Sweden both
pig iron and scrap with extremely low phosphorus and sulphur contents are
used for the acid process.
The ratios between the pig iron and the scrap vary considerably, according
to the supply of raw material and the purpose for which the product is intended.
The charge may be, for example, 73 % of pig iron + 7 % of scrap 4- 20 % of
ore, or, at the opposite extreme, 26 % of pig iron + 74 % of scrap.
P ig iron for the acid open-hearth process contains as a rule from 0*50 to
0*76 % of silicon. The finery ore should contain as much iron as possible. Ore
of this kind often contains from 65 to 70 Y„ of iron.