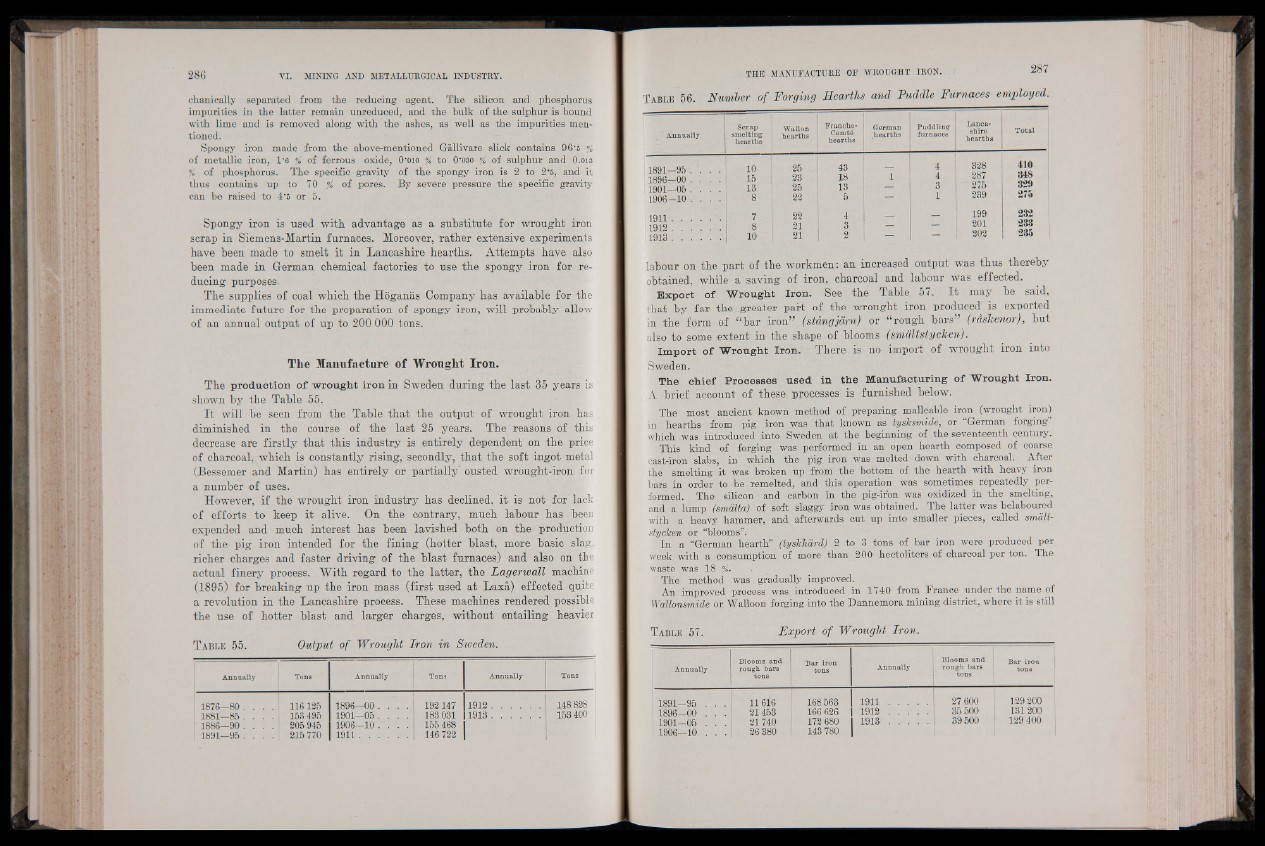
chanically separated from the reducing agent. The silicon and phosphorus
impurities in the latter remain unreduced, and the bulk of the sulphur is bound
with lime and is removed along with the ashes, as well as the impurities mentioned.
Spongy iron made from the above-mentioned Gallivare slick contains 96'6 %
of metallic iron, I -« % of ferrous oxide, O'oio % to 0'030 % of sulphur and O.013
% of phosphorus. The specific gravity of the spongy iron is 2 to 2'6, and it
thus contains up to 70 % of pores. By severe pressure the specific gravity
can be raised to 4 ‘6 or 5.
Spongy iron is used with advantage as a substitute for wrought iron
scrap in Siemens-Martin furnaces. Moreover, rather extensive experiments
have been made to smelt it in Lancashire hearths. Attempts have also
been made in German chemical factories to use the spongy iron for reducing
purposes.
The supplies of coal which the Hoganas Company has available for the
immediate future for the preparation of spongy iron, will probably allow
of an annual output of up to 2 0 0 0 0 0 tons.
The Manufacture of Wrought Iron.
The production of wrought iron in Sweden during the last 35 years is
shown by the Table 55.
It will be seen from the Table that the output of wrought iron has
diminished in the course of the last 25 years. The reasons of this
decrease are firstly that this industry is entirely dependent on the price
of charcoal, which is constantly rising, secondly, that the soft ipgot metal
(Bessemer and Martin) has entirely or partially ousted wrought-iron for
a number of uses.
However, if the wrought iron industry has declined, it is not for lack
of efforts to keep it alive. On the contrary, much labour has been
expended and much interest has been lavished both on the production
of the pig iron intended for the fining (hotter blast, more basic slag,
richer charges and faster driving, of the blast furnaces) and also on the
actual finery process. With regard to the latter, the Lagerwall machine
(1895) for breaking up the iron mass (first used at Laxa) effected quite
a revolution in the Lancashire process. These machines rendered possible
the use of hotter blast and larger charges, without entailing heavier
T able 55. Output of Wrought Iron in Sweden.
Annually Tons Annually Tona Annually Tons
1876—80 . . . .
1881—85 . . . .
1886—90 . . . .
1891—95 . . . .
116 125
153 495
205 945
215 770
1896—00 . . . .
1901—05 . . . .
1906—10 . . . .
1911....................
192 147
183 031
155 468
146 722
191 2 ................
191 3 ................
148 828 1
153 400 !
f&s
T able 56. Number of Forging Hearths and Puddle Furnaces employed.
Annually
S c rap .
smelting
hearths
Wallon
hearths
Franche-
Cojnté
hearths
German
.hearths
Fuddling
furnaces
Lancashire
hearths
Total
1891-95 . '. . .
1896—00 ............
1901 05 : . . .
— . 1
10
15
’ . 13
8
25
23
25
. 22
43
18
13
5 -
1 43
1
328
287
~ 275
239
410
348
329
275
191 1 ............ 1
191 2 ................
11913....................
8
10
22
21
21
432
— 199
201
202
232
233
235
labour on the part of the workmen: an increased output was thus thereby
obtained, while aT saving of iron, charcoal and labour was effected.
Export of Wrought Iron. See the Table 57. It may be said,
that by far the greater part of the wrought iron produced is exported
in the form of “bar iron” (stangjarn) or “ rough bars” (raskenor), but
also to some extent in the shape of blooms (smdltstycken).
Import of Wrought Iron. There is no import of wrought iron into
Sweden.
The chief Processes used in the Manufacturing of Wrought Iron.
A brief account of these processes is furnished below.
The most ancient known method of preparing malleable iron (wrought iron)
in hearths from pig iron was that known as tysksmide, or “German forging”
which was introduced into Sweden at the beginning of the seventeenth century.
This kind of forging was performed in an open hearth composed of coarse
cast-iron slabs, in which the pig iron was melted down with charcoal. After
the smelting it was broken up from the bottom of the hearth with heavy iron
bars in order to be remelted, and this operation was sometimes repeatedly performed.
The silicon and carbon in the pig-iron was oxidized in the smelting,
and a lump (smdlta) of soft slaggy iron was obtained. The latter was belaboured
with a heavy hammer, and afterwards cut up into smaller pieces, called smdltstycken
or “blooms”.
In a “German hearth” (tyskhard) 2 to 3 tons of bar iron were produced per
week with a consumption of more than 200 hectoliters of charcoal per ton. The
waste was 18 %.
The method was gradually improved.
An improved process was introduced in 1740 from France under the name of
Wallonsmide or Walloon forging into the Dannemora mining district, where it is still
T able 57. Export of Wrought Iron.
Annually
Blooms and
rough bars
tons
Bar iron
tons
Blooms and
Annually rough bars
tons
Bar iron
tons
1891—95 . . . 11616 168 563 1911 ................ 27 600 129 200
1896—00 . . . 21453 166 626 1912 . . . 35 500 131200
1901—05 . . . 21740 172 680 1913 ................ 39500 129 400
1 1906—10 . . . 26 380 143 780