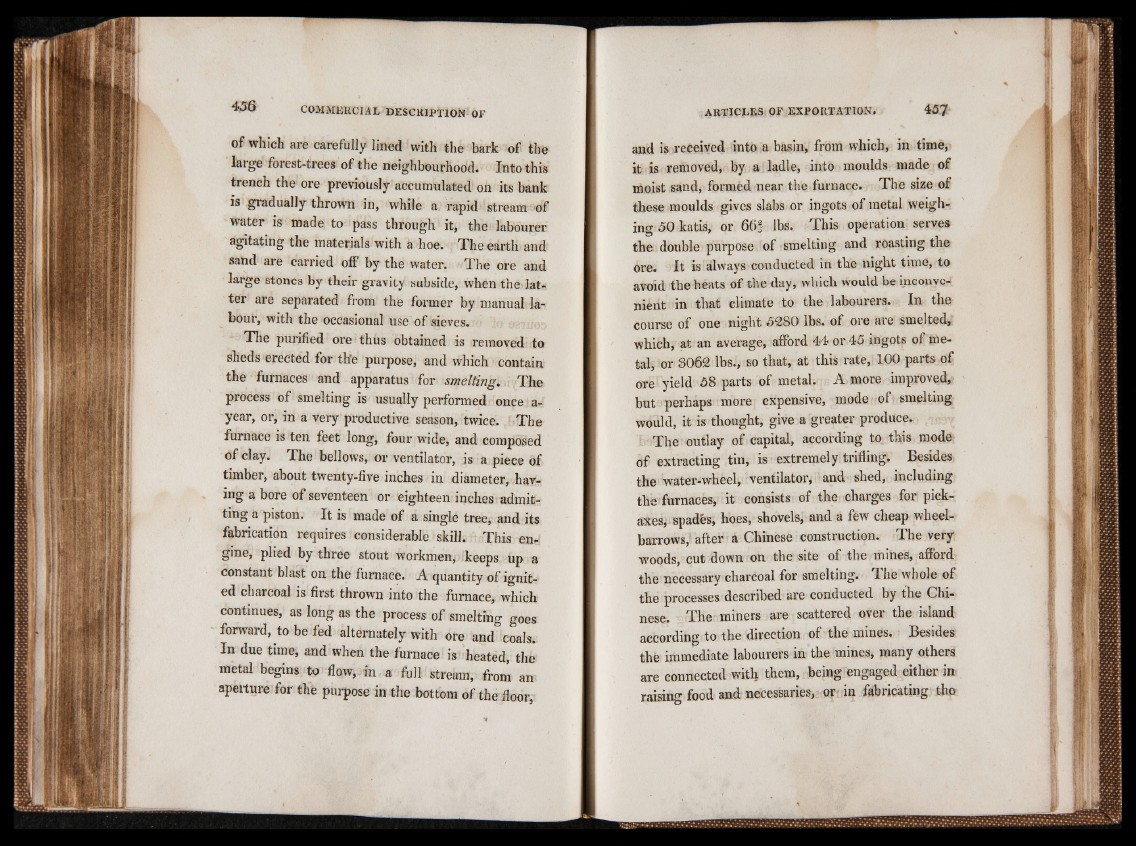
of which are carefully lined with the bark of the
forge forest-trees of the neighbourhood. Into this
trench the ore previously accumulated on its bank
is gradually thrown in, while a. rapid stream of
water is made to pass through it, the labourer
agitating the materials with a hoe. The earth and
sand are carried off by the water. The ore and
forge stones by their gravity subside, when the latter
are separated from the former by manual labour,
with the occasional use of sieves.
The purified ore thus obtained is removed to
sheds erected for the purpose, and which contain
the furnaces and apparatus for smelting. The
process of smelting is usually performed once a-
year, or, in a very productive season, twice. The
furnace is ten feet long, four wide, and composed
of clay. The bellows, or ventilator, is a piece of
timber, about twenty-five inches in diameter, having
a bore of seventeen or eighteen inches admitting
a piston. It is made of a single tree, and its
fabrication requires considerable skill. This engine,
plied by three stout workmen, keeps up a
constant blast on the furnace. A quantity of ignited
charcoal is first thrown into the furnace, which
continues, as long as the process of smelting goes
forward, to be fed alternately with ore and coals.
In due time, and when the furnace is heated, the
metal begins to flow, in a full stream, from an
aperture for the purpose in the bottom of the floor,
ARTICLES OF EXPORTATION
and is received into a basin, from which, in time,
it is removed, by a ladle, into moulds made of
moist sand, formed near the furnace. The size of
these moulds gives slabs or ingots of metal weighing
50 katis, or 665 lbs. This operation serves
the double purpose of smelting and roasting the
ore. It is always conducted in the night time, to
avoid the heats of the day, which would be inconvenient
in that climate to the labourers. In the
course of one night 5280 lbs. of ore are smelted,
which, at an average, afford 44 or 45 ingots of metal,
or 3062 lbs., so that, at this rate, 100 parts of
ore’ yield 58 parts of metal. A more improved,
but perhaps more expensive, mode of smelting
would, it is thought, give a greater produce.
The outlay of capital, according to. this mode
of extracting tin, is extremely trifling. Besides
the water-wheel, ventilator, and shed, including
the furnaces, it consists of the charges for pick-,
axes, spades, hoes, shovels, and a few cheap wheelbarrows,
after a Chinese construction. The very
woods, cut down on the site of the mines, afford
the necessary charcoal for smelting. The whole of
the processes described are conducted by the Chinese.
The miners are scattered over the island
according to the direction of the mines. Besides
the immediate labourers in the mines, many others
are connected with them, being engaged either in
raising food and necessaries, or in fabricating the