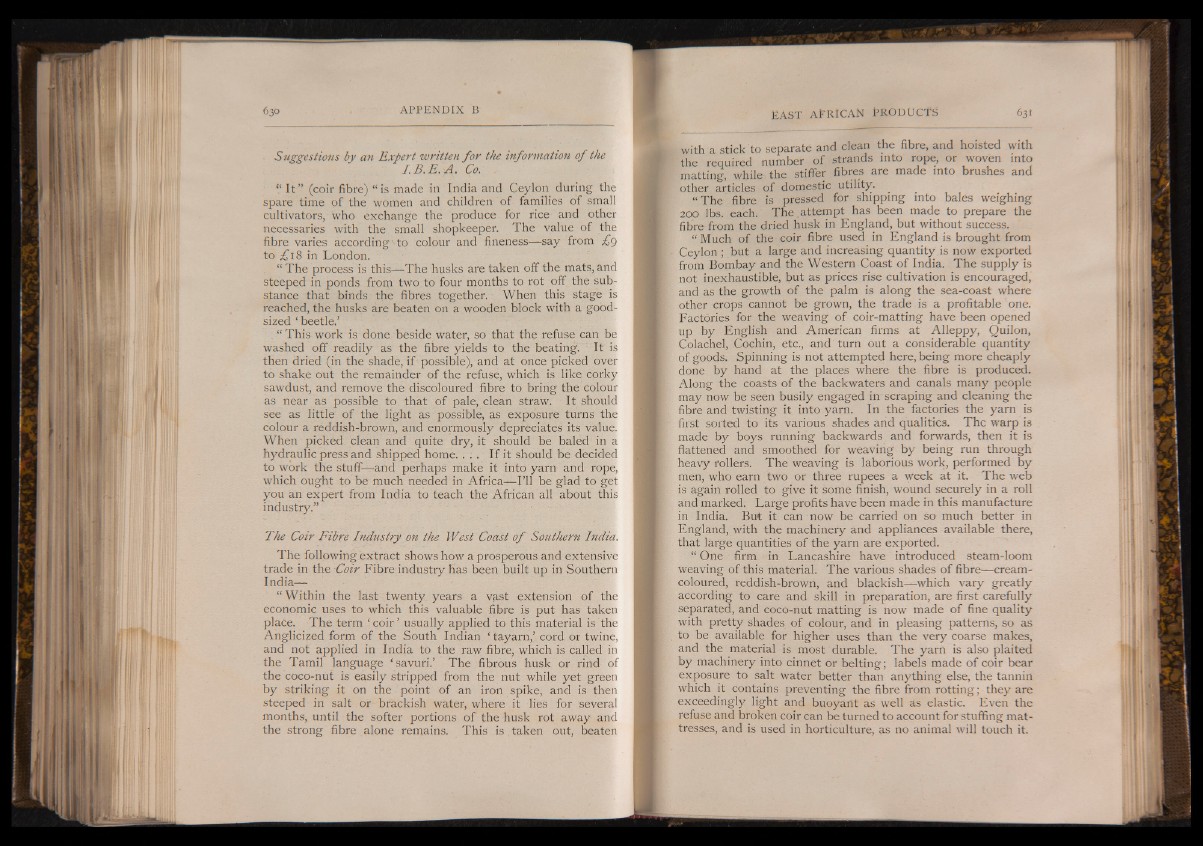
Suggestions by an Expert written fo r the information o f the
I .B .E .A . Co.
“ I t ” (coir fibre) “ is made in India and Ceylon during the
spare time of the women and children of families of small
cultivators, who exchange the produce for rice and other
necessaries with the small shopkeeper. The value of the
fibre varies according'-to colour and fineness— say from £9
to ^18 in London.
“ The process is this— The husks are taken off the mats, and
steeped in ponds from two to four months to rot off the substance
that binds the fibres together. When this stage is
reached, the husks are beaten on a wooden block with a good-
sized ‘ beetle.’
. “ This work is done beside water, so that the refuse can be
washed off readily as the fibre yields to the beating. : It is
then dried (in the shade, if possible), and at once picked over
to shake out the remainder of the refuse, which is like corky
sawdust, and remove the discoloured fibre to bring the colour
as near as possible to that of pale, clean straw. It should
see as little of the light as possible, as exposure turns the
colour a reddish-brown, and enormously depreciates its value.
When picked clean and quite dry, it should be baled in a
hydraulic press and shipped home. . . . I f it should be decided
to work the stuff—-and perhaps make it into yarn and rope,
which ought to be much needed in Africa— I’ll be glad to get
you an expert from India to teach the African all about this
industry.”
The Coir Fibre Industry on the West Coast o f Southern India.
The following extract shows how a prosperous and extensive
trade in the Coir Fibre industry Has been built up in Southern
India—
“ Within the last twenty years a v£.st extension of the
economic uses to which this valuable fibre is put has taken
place. The term ‘ coir’ usually applied to this material is the
Anglicized form of the South Indian ‘ tayarn,’ cord or twine,
and not applied in India to the raw fibre, which is called in
the Tamil language ‘ savuri.’ The fibrous husk or rirtd of
the coco-nut is easily stripped from the nut while yet green
by striking it on the point of an iron spike, and is then
steeped in salt or brackish water, where it lies for several
months, until the softer portions of the husk rot away and
the strong fibre alone remains. This is taken out, beaten
with a stick to separate and clean the fibre, and hoisted with
the required number of strands into rope, or woven into
matting, while the stiffer fibres are made into brushes and
other articles of domestic utility.
“ The fibre is pressed for shipping into bales weighing
200 lbs. each. The.attempt has been made to prepare the
fibre from the dried husk in England, but without success.
“ Much of the coir fibre used in England is brought from
Ceylon ; but a large and increasing quantity is now exported
from Bombay and the Western Coast of India. The supply is
not inexhaustible, but as prices rise cultivation is encouraged,
and as the growth of the palm is along the sea-coast where
other crops cannot be grown, the trade is a profitable one.
Factories for the weaving of coir-matting have been opened
up by English and American firms, at Alleppy, Quilon,
Colachel, Cochin, etc., and turn out a considerable quantity
of goods. Spinning is not attempted here, being more cheaply
done by hand at the places where the fibre is produced.
Along the coasts of the backwaters and canals many people
may now be seen busily engaged in scraping and cleaning the
fibre and twisting it into yarn. In the factories the yarn is
first sorted to its various shades and qualities. The warp is
made by boys running backwards and forwards, then it is
flattened and smoothed for weaving by being run through
heavy rollers. The weaving is laborious work, performed by
men, who earn two or three rupees a week at it. The web
is again rolled to give it some finish, wound securely in a roll
and marked. Large profits have been made in this manufacture
in India. But it can now be carried on so much better in
England, with the machinery and appliances available there,
that large quantities of the yarn are exported.
“ One firm in Lancashire have introduced steam-loom
weaving of this material. The various shades of fibre— cream-
coloured, reddish-brown, and blackish— -which vary greatly
according to care and skill in preparation, are first carefully
separated, and coco-nut matting is now made of fine quality
with pretty shades of colour, and in pleasing patterns, so as
to be available for higher uses than the very coarse makes,
and the material is most durable. The yarn is also plaited
by machinery into cinnet or belting; labels made of coir bear
exposure to salt water better than anything else, the tannin
which it contains preventing the fibre from rotting; they are
exceedingly light and buoyant as well as elastic. Even the
refuse and broken coir can be turned to account for stuffing mattresses,
and is used in horticulture, as no animal will touch it.