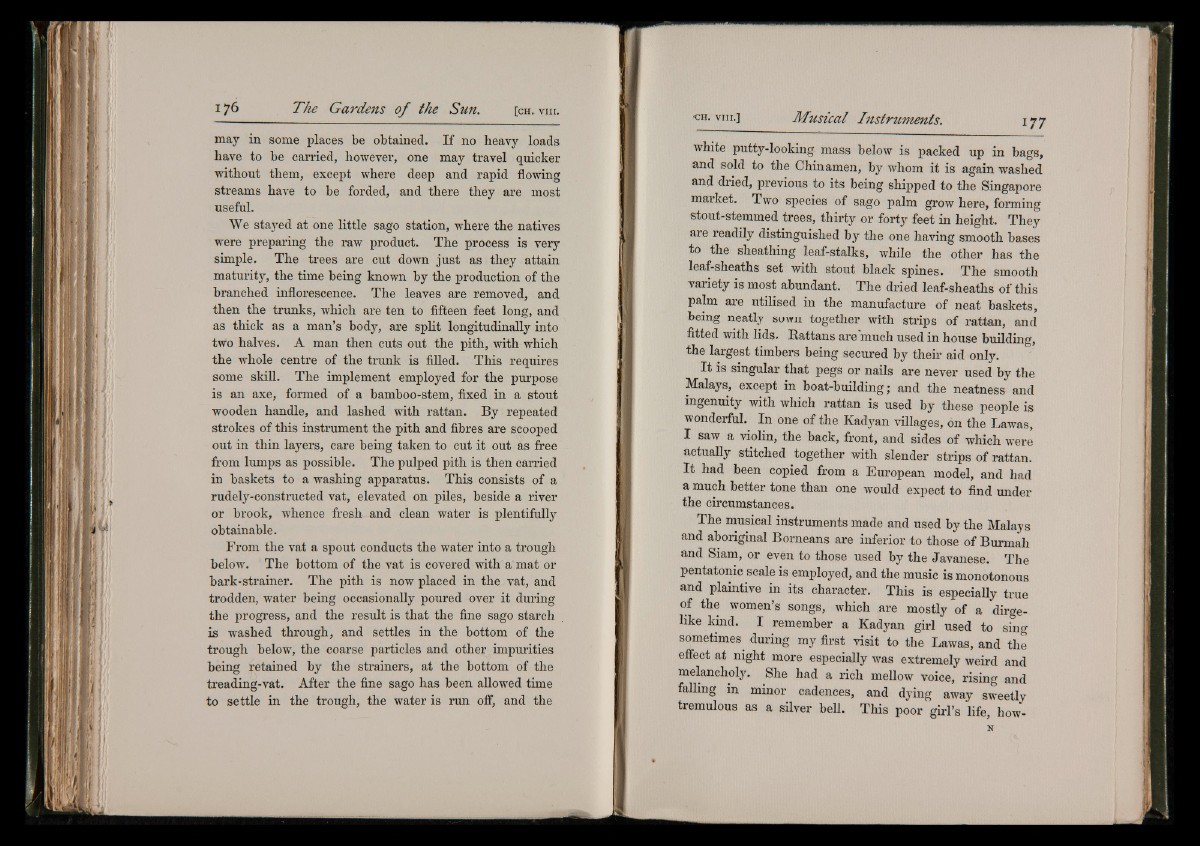
may in some places be obtained. If no heavy loads
have to be carried, however, one may travel quicker
without them, except where deep and rapid flowing
streams have to be forded, and there they are most
useful.
We stayed at one little sago station, where the natives
were preparing the raw product. The process is very
simple. The trees are cut down just as they attain
maturity, the time being known by the production of the
branched inflorescence. The leaves are removed, and
then the trunks, which are ten to fifteen feet long, and
as thick as a man’s body, are split longitudinally into
two halves. A man then cuts out the pith, with which
the whole centre of the trunk is filled. This requires
some skill. The implement employed for the purpose
is an axe, formed of a bamboo-stem, fixed in a stout
wooden handle, and lashed with rattan. By repeated
strokes of this instrument the pith and fibres are scooped
out in thin layers, care being taken to cut it out as free
from lumps as possible. The pulped pith is then carried
in baskets to a washing apparatus. This consists of a
rudely-constructed vat, elevated on piles, beside a river
or brook, whence fresh and clean water is plentifully
obtainable.
From the vat a spout conducts the water into a trough
below. The bottom of the vat is covered with a mat or
bark-strainer. The pith is now placed in the vat, and
trodden, water being occasionally poured over it during
the progress, and the result is that the fine sago starch
is washed through, and settles in the bottom of the
trough below, the coarse particles and other impurities
being retained by the strainers, at the bottom of the
treading-vat. After the fine sago has been allowed time
to settle in the trough, the water is run off, and the
white putty-looking mass below is packed up in bags,
and sold to the Chinamen, by whom it is again washed
and dried, previous to its being shipped to the Singapore
market. Two species of sago palm grow here, forming
stout-stemmed trees, thirty or forty feet in height. They
are readily distinguished by the one having smooth bases
to the sheathing leaf-stalks, while the other has the
leaf-sheaths set with stout black spines. The smooth
variety is most abundant. The dried leaf-sheaths of this
palm are utilised in the manufacture of neat baskets,
being neatly sown together with strips of rattan, and
fitted with lids. Battans are much used in house building,
the largest timbers being secured by their aid only.
It is singular that pegs or nails are never used by the
Malays, except in boat-building ; and the neatness and
ingenuity with which rattan is used by these people is
wonderful. In one of the Kadyan villages, on the Lawas,
I saw a violin, the back, front, and sides of which were
actually stitched together with slender strips of rattan.
It had been copied from a European model, and had
a much better tone than one would expect to find under
the circumstances.
The musical instruments made and used by the Malays
and aboriginal Borneans are inferior to those of Burmali
and Siam, or even to those used by the Javanese. The
pentatonic scale is employed, and the music is monotonous
and plaintive in its character. This is especially true
of the women’s songs, which are mostly of a dirgelike
kind. I remember a Kadyan girl used to sing
sometimes^ during my first visit to the Lawas, and the
effect at night more especially was extremely weird and
melancholy. She had a rich mellow voice, rising and
falling in minor cadences, and dying away sweetly
tremulous as a silver bell. This poor girl’s life, how-
N